Aluminium Hydroxide Powder for Flame Retardants: Surface Modification Explained
Date: May-13-2025 Categories: News、Aluminium Hydroxide Views: 131
Aluminium hydroxide powder is a widely used material with many functions—especially as a flame retardant, smoke suppressant, and filler. It is known for working well with other flame-retardant substances like phosphorus, creating a synergistic effect that boosts performance. Thanks to its non-toxic and eco-friendly nature, aluminium hydroxide is heavily used in electronics, chemicals, cables, plastics, rubber, and other industries.
However, to achieve a good flame-retardant effect, a high amount—40% to 60%—of aluminium hydroxide needs to be added. This can negatively affect the product’s mechanical strength and processing performance, especially during extrusion. To solve this issue and expand its application in polyolefins and similar materials, aluminium hydroxide must be surface modified.
1. Common Surface Modifiers for Aluminium Hydroxide
(1) Silane Coupling Agent
Silane coupling agents are a large group of chemicals—over a hundred types—used to bond organic and inorganic materials. Based on the structure of their R functional groups, silanes are categorized as α-functional, β-functional, and γ-functional types.
γ-functional silanes are the most stable and suitable for both thermoplastics and thermosets, significantly improving product strength.
α-functional silanes are also stable and can enhance mechanical, electrical, and moisture-resistant properties. Products modified with α-silanes are often used in cables and wires.
(2) Zirconium Coupling Agent
Zirconium-based agents are inorganic polymers that contain zirconium aluminate. These agents have two organic ligands—one ensures hydroxyl stability, and the other boosts organic reactivity. They work well for modifying ultrafine aluminium hydroxide powder.
(3) Advanced Fatty Acids and Salts
These are among the earliest modifiers used. Common examples include stearic acid and metal stearates. One end of the molecule has a long alkyl chain, while the other has a reactive carboxyl group. They improve the compatibility between aluminium hydroxide and polymers, enhancing mechanical strength and processing ability.
(4) Unsaturated Organic Acids
These acids contain double bonds and hydroxyl groups, usually with fewer than 10 carbon atoms. Common types include acrylic acid, methacrylic acid, and cinnamic acid. The stronger the acid, the easier it forms ionic bonds with aluminium hydroxide. They are effective when dealing with aluminium hydroxide containing alkali metal ions.
(5) Silicone
Known as silicone oils, these are polymers with a Si-O-Si backbone. Popular types include hydrogen-containing polymethylsiloxane and hydroxyl-terminated polydimethylsiloxane. These materials enhance the surface compatibility of aluminium hydroxide with various plastics.
2. Surface Modification Methods
There are two main methods for modifying the surface of ultrafine aluminium hydroxide powder: dry modification and wet modification.
(1) Dry Modification
In this method, the powder is preheated. A modifier is slowly added during high-speed mixing. After the reaction time, the product is packaged.
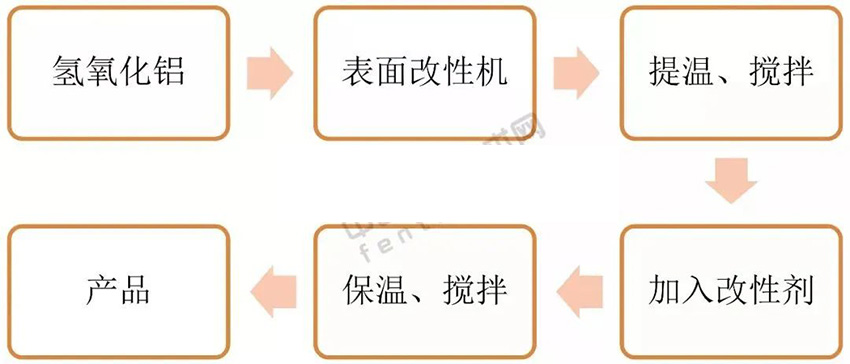
Pros: Simple setup and low equipment cost.
Cons: Dust pollution, high labor intensity, low efficiency, only 10% coating rate, and unstable performance.
(2) Wet Modification
Here, the aluminium hydroxide slurry is filtered and washed. The filter cake is then pulped and treated with a modifier at a controlled temperature. After mixing, the material is filtered, dried, and packaged.
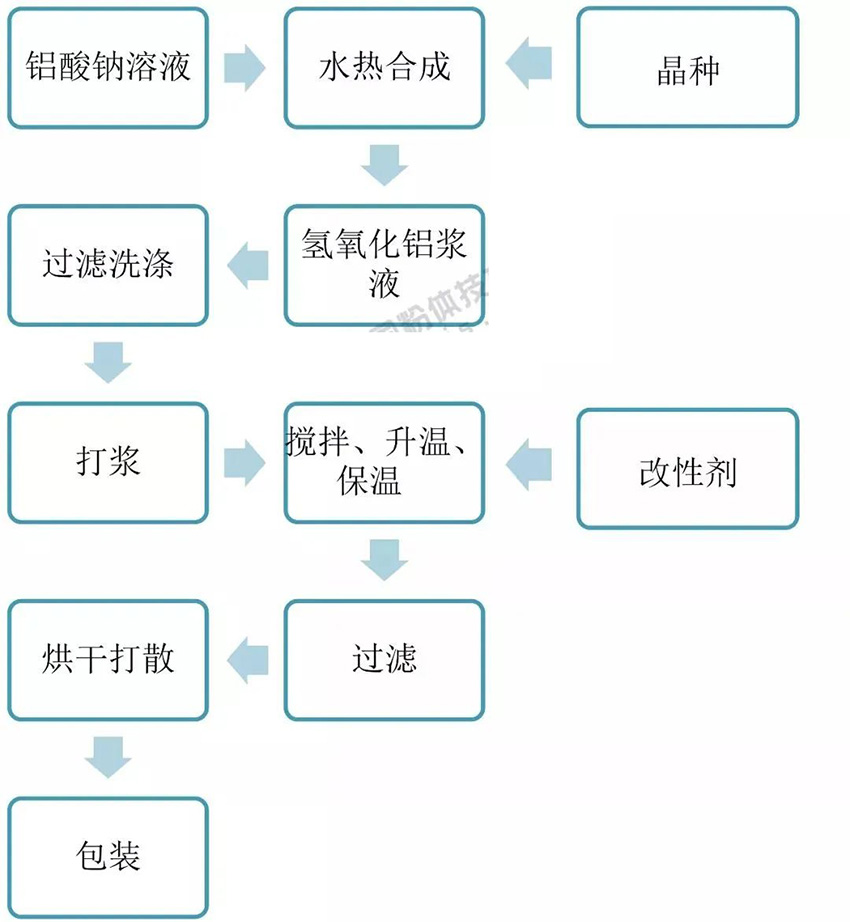
Pros: Cleaner process, higher efficiency, 20–30% coating rate, and better performance.
Cons: Requires more equipment and longer process time. Despite the complexity, wet modification is becoming more popular due to its effectiveness.
Before diving into surface treatment methods, it helps to review the core characteristics of ATH. Read What is Alumina Trihydrate (ATH)?
3. How to Evaluate Surface Modification
To assess how well the surface modification works, several tests are commonly used:
(1) Oil Absorption Rate
This test checks how much castor oil is needed to fully wet the powder. After modification, the oil absorption usually decreases, showing better compatibility. For instance, silane-modified powder may have a 10% lower oil absorption rate.
(2) SEM (Scanning Electron Microscope) Test
Electron microscopy allows you to see how well the particles are dispersed in the polymer. Modified powders typically show better dispersion.
(3) FTIR (Fourier Transform Infrared Spectroscopy)
This test is used to identify chemical groups on the powder surface. For example, if methyl vinyl silane is used, you can detect vinyl (-Vi) and silicon (-Si) groups in the modified material.
(4) Product Performance Testing
Products made from both modified and unmodified powders are tested for:
Oxygen index (flame retardancy)
Tensile strength
Elongation at break
Improved properties in these tests indicate successful surface modification.
(5) Activation Index
This test measures the amount of powder that floats on water after treatment, showing how hydrophobic the powder is. Some modifiers like sodium stearate, titanate, or hydrophobic silane increase floating, indicating good surface activation. However, this test isn’t suitable for hydrophilic modifiers. In those cases, FTIR remains the more accurate method.
Aluminium hydroxide powder is a versatile flame retardant that becomes even more effective after surface modification. By selecting the right modifiers and treatment method (wet or dry), manufacturers can significantly improve the performance, processing, and application range of aluminium hydroxide in plastic, rubber, cable, and electronic products.