Calcined Alumina Polishing: Precision Surface Finishing for Metals, Ceramics & Glass
Date: May-15-2025 Categories: News、Alumina、Aluminium Hydroxide Views: 240
Introduction
In industries such as aerospace, electronics, and advanced manufacturing, surface quality isn’t just aesthetic—it’s essential. Whether you're working with metals, ceramics, or glass, achieving a smooth, scratch-free, and dimensionally stable finish is critical for both functionality and durability. That’s where calcined alumina polishing comes in.
Calcined alumina, or calcined aluminum oxide (Al₂O₃), is a premium-grade polishing material known for its hardness, chemical purity, and controlled particle size. Its unique physical and chemical properties make it one of the most effective abrasives for precision polishing applications.Learn more from Wikipedia on Aluminium Oxide.
What Is Calcined Alumina?
Calcined Alumina is produced by heating aluminum hydroxide to temperatures between 1,100–1,500 °C, removing bound water and transforming it into crystalline α-alumina. The result is a fine, white, high-purity powder with excellent thermal stability, high hardness (Mohs hardness ~9), and outstanding chemical inertness.
Key Benefits of Calcined Alumina for Polishing
- High Hardness and Abrasive Power
With a Mohs hardness of around 9, calcined alumina effectively eliminates micro-surface defects, scratches, and contaminants from hard surfaces like ceramics and metals. - Controlled Particle Size Distribution
Available in D50 sizes ranging from 0.5 μm to 10 μm, it supports both rough and fine polishing. The uniform particle size ensures flawless finishes without deep scratches. - Thermal and Chemical Stability
Unlike softer abrasives that degrade under high-speed polishing, calcined alumina maintains its structural integrity even under extreme heat and pressure—providing consistent performance. - High Purity, Low Contamination
With purity levels exceeding 99.5%, calcined alumina is safe for use on sensitive surfaces like optical glass, semiconductors, and biomedical ceramics.
Applications of Calcined Alumina Polishing
- Metal Surface Finishing: Enhances reflectivity and smoothness in stainless steel, titanium alloys, aluminum, and precision castings.
- Ceramic Polishing: Ideal for advanced ceramics such as alumina, zirconia, and silicon carbide—used in electronics, medical devices, and aerospace.
- Glass Polishing: Achieves scratch-free, high-gloss finishes in LCD panel, optical lens, and architectural glass applications.
- Polishing Slurries and Compounds: A key ingredient in CMP slurries and polishing pastes due to its abrasive strength and dispersibility.
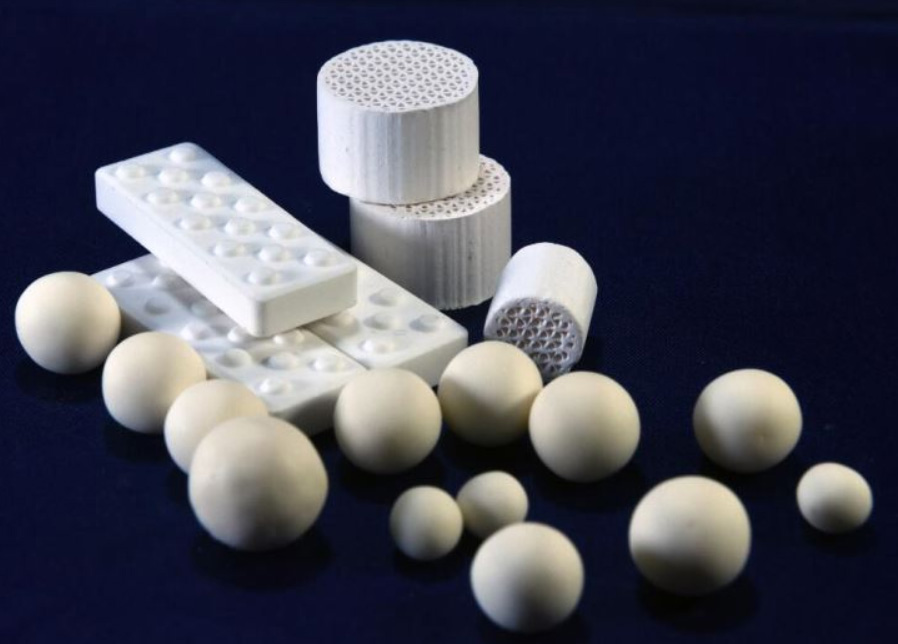
Technical Specifications from Banlan Chem
Parameter | Specification Range |
---|---|
Purity (Al₂O₃) | ≥ 99.5% |
Particle Size (D50) | 0.3 µm – 5 µm |
Surface Area (BET) | 3 – 6 m²/g |
Moisture Content | < 0.1% |
Bulk Density | 0.8 – 1.2 g/cm³ |
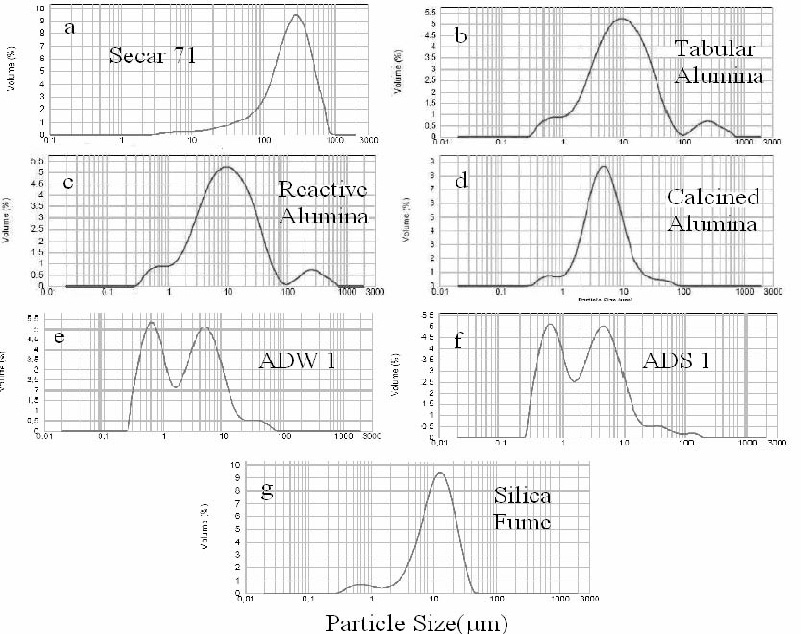
Calcined Alumina vs. Fused Alumina
Feature | Calcined Alumina | Fused Alumina |
---|---|---|
Structure | Porous, fine-grain | Dense, crystalline |
Polishing Action | Gentle, uniform | More aggressive |
Heat Generation | Lower | Higher |
Surface Finish | Smoother | Rougher |
Advantages Over Other Polishing Materials
- Compared to Silica: Greater hardness and faster material removal with fewer steps.
- Compared to Cerium Oxide: Offers broader compatibility and better cost-performance.
- Compared to Diamond Powder: Less aggressive and more cost-effective for mid-range finishing needs.
Packaging & Supply
- 25 kg kraft paper bags with PE liner
- 500 kg jumbo bags (bulk orders)
- OEM/private-label packaging available
- Global export with COA, MSDS, and REACH documentation
All products are strictly tested to ensure consistency in particle size, purity, and performance across batches.
Industries Served
- Electronics and semiconductor polishing
- Automotive metal finishing
- Precision optics manufacturing
- Biomedical ceramic production
- Abrasive tool manufacturing
- Glass processing and polishing pad production
How to Use Calcined Alumina for Polishing
- Dry Powder: Use rotary polishers, felt pads, or abrasive belts—ideal for metal parts and castings.
- Polishing Slurry: Mix with deionized water or dispersants for use in automated polishing systems.
- Compound Form: Blend with wax, oil, or polymer bases to produce polishing bars or pastes.
⚠️ Always use adequate ventilation and dust protection when handling fine powders.
FAQs About Calcined Alumina Polishing
Q: Can it be used for automated polishing lines?
A: Yes, it is suitable for rotary and vibratory systems.
Q: Does it leave residue?
A: No, it produces a clean finish with minimal cleanup.
Q: What’s the ideal storage method?
A: Store in a sealed, moisture-proof container at room temperature.
Conclusion
Calcined alumina polishing offers a balanced combination of performance, consistency, and cost-efficiency for precision surface finishing. Its high purity, exceptional hardness, and versatility make it the top choice for manufacturers and engineers who demand impeccable surface quality.
Whether you're refining stainless steel, advanced ceramics, or optical-grade glass, our high-purity calcined alumina delivers outstanding results.
📩 Contact us today for technical data sheets, samples, or custom formulation support.
Request a Sample or Quote
If you're looking for a consistent polishing solution, BanlanChem is your trusted partner. Contact us today to request samples, get datasheets, or consult with our experts.