Product Overview
Low sodium calcined alumina is a high-purity aluminum oxide (Al₂O₃) powder characterized by its low sodium (Na₂O) content, high hardness, and excellent thermal and chemical stability. It is produced by calcining high-grade aluminum hydroxide under controlled temperature conditions to achieve a dense, alpha-phase alumina structure with minimal impurity levels—especially low in alkali metals.
Key Features
- Low Sodium Content: ≤ 0.03%
- High Alpha-Alumina Phase: >99%
- High Purity: Al₂O₃ ≥ 99.6%
- Controlled Particle Size: Available in fine to ultra-fine grades
- Excellent Dispersibility and Reactivity
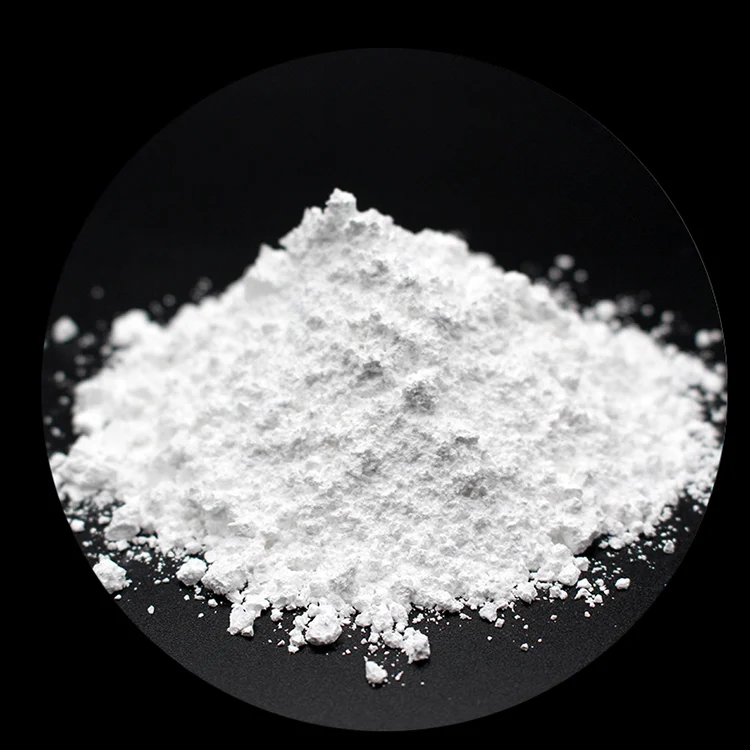
Technical Specifications
Identification of grades
1) Calcined Aluminum S-100 grades: White granular free flowing powder passes through 150 m.
2) Calcined Aluminum S-300 grade: White superfine powder passes though 45 micron.
3) Calcined Alumina SCM grade: It is finally ground grades consisting entirely of superfine passes through 45 micron.
4) Calcined Alumina S-300 PT: It is finely ground grade consisting entirely of superfine with surface treated.
Low Sodium Calcined Alumina
Characteristics: with high quality raw materials and advanced production technology, the products have the advantages of low sodium oxide, high conversion rate and fine particle morphology.
Application: all kinds of abrasives, abrasives and various wear-resisting filler, various ceramic and refractory alumina micro-powder, high purity structure ceramics, electronic components, high frequency insulating porcelain.
Brand | Chemical composition(%) | α-Al2O3 | Effective density | Primary crystal size | ||||
Al2O3 ≥ | SiO2 ≤ | Fe2O3≤ | Na2O≤ | L.O.I≤ | % ≥ | ≥ | μm | |
AC-200MS | 99.0 | 0.10 | 0.04 | 0.2 | 0.2 | 93 | 3.93 | 2.5±1 |
AC-200MS | 99.0 | 0.10 | 0.04 | 0.2 | 0.2 | 94 | 3.93 | 4±1 |
Brand | Chemical composition(%) | α-Al2O3 | Particle size | ||||
Al2O3≥ | SiO2≤ | Fe2O3≤ | Na2O≤ | L.O.I≤ | %≥ | μm | |
ACG-200MS | 99.0 | 0.20 | 0.04 | 0.2 | 0.2 | 92 | 1-2 |
ACG-200MS | 99.0 | 0.20 | 0.04 | 0.2 | 0.2 | 93 | 3-5 |
Fine Powder Of Low Soda Calcined Aluminua (Tunnel Kiln)Fine Powder Of Low Soda Calcined Alumina
Characteristics: the products have the advantages of high conversion rate, controllable crystal morphology, good thermal shock resistance, stable high temperature performance and stable shrinkage rate of products.
Application: it is widely used in advanced refractories, structural ceramics, functional ceramics, metal composite ceramics, thermal conductive ceramics and other fields.
Brand | Chemical composition(%) | α-Al2O3 | BET | Particle size | ||||
Al2O3≥ | SiO2≤ | Fe2O3≤ | Na2O≤ | L.O.I≤ | %≥ | m2/g | μm | |
AC-10LS | 99.5 | 0.1 | 0.04 | 0.1 | 0.2 | 93 | 4-7 | ≤1 |
T1 | 99.5 | 0.1 | 0.04 | 0.1 | 0.1 | 95 | 1.6-2.0 | 2.5-3.2 |
T2 | 99.5 | 0.1 | 0.04 | 0.1 | 0.1 | 95 | 1.2-1.5 | 4.0-5.5 |
T3 | 99.5 | 0.1 | 0.04 | 0.1 | 0.1 | 95 | 1.3-1.6 | 3.5-4.5 |
T4 | 99.5 | 0.1 | 0.04 | 0.1 | 0.1 | 95 | 1.5-3.5 | 2.0-3.0 |
Applications
- Ceramic Substrates & Spark Plugs
- High-Purity Refractories
- Electronic Ceramics & Capacitors
- Glass & Glazes with High Clarity Requirements
- Alumina Coatings in Li-ion Batteries
- Catalyst Carriers & Fine Polishing Materials
Why Choose BanLanChem’s Low Sodium Calcined Alumina?
BanLanChem provides low sodium alumina with stable quality and customizable particle sizes. Our advanced calcination technology ensures ultra-low Na₂O content, meeting the requirements of sensitive industries such as electronics and batteries.
Packaging & Storage
- 25kg bags or 1000kg jumbo bags
- Store in dry, cool conditions
- Shelf life: 12 months
Related Products
Comparison with Other Alumina Grades
Low Sodium Calcined Alumina vs Regular Calcined Alumina
Property | Low Sodium | Regular |
---|---|---|
Na₂O Content | ≤ 0.03% | 0.1%–0.3% |
Purity | ≥ 99.6% | 98.5%–99.5% |
Applications | Electronics, batteries | General polishing, refractories |
Price | Higher | Lower |
Low Sodium Calcined Alumina vs Tabular Alumina
Property | Low Sodium Calcined Alumina | Tabular Alumina |
---|---|---|
Production Process | Calcined (1000–1300°C) | Sintered (>1800°C) |
Form | Fine Powder | Fused Aggregate |
Applications | Electronics, coatings | Refractories |
FAQ
What is low sodium calcined alumina?
It is a high-purity alumina powder with ≤0.03% Na₂O, used in applications where low alkali content is critical.
How is it different from regular calcined alumina?
Low sodium grades contain significantly less sodium and other alkali impurities, making them ideal for high-tech applications.
Do you offer custom sizes?
Yes, D50 from 1μm to 10μm is available depending on application requirements.
Is it suitable for lithium battery coating?
Yes. Its low impurity content and high thermal stability make it perfect for use in lithium-ion battery materials.